Recent Photos
Explore complete photo collection
Tuesday, July 28, 2009
Moving
Thursday, April 9, 2009
Formula Hybrid Testing
Failing the sound test by 1db, but it's an easy fix
A quick video of us driving on internal combustion engine only. With the electric system entirely shut off it should still be faster than the winner last year.
Formula Hybrid Assembly

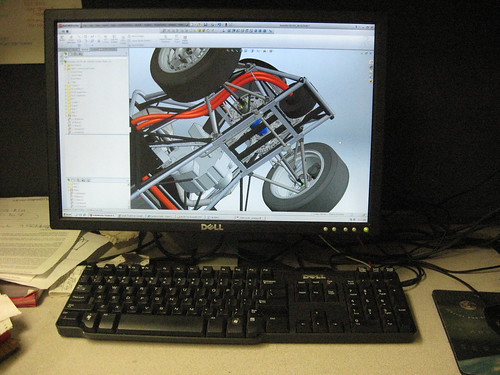
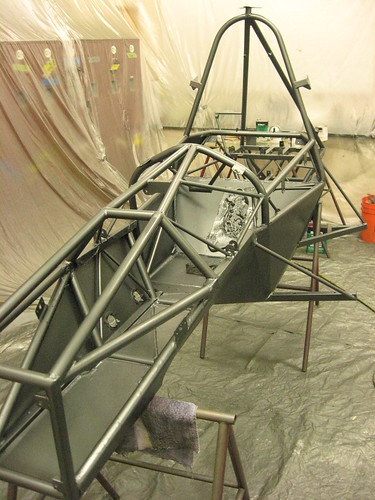
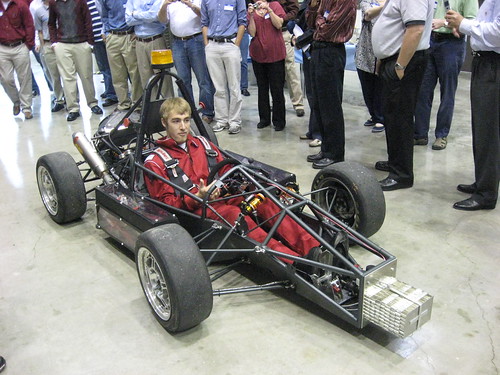
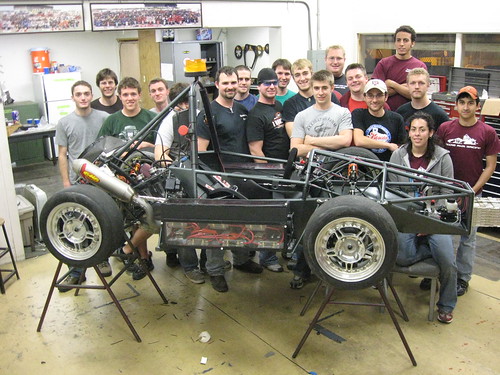
The car and the team completely assembled
Here is a little video of the assembly of the car:
Monday, March 2, 2009
Climbing at Reimer's Ranch
Reimer's Ranch is a very small county park that caters to limestone climbing and Mountain Bikers. On a busy day you might see 20 or 30 cars in the gravel parking lot. It costs $8 per car, and there is no camping allowed. There are well over 100 climbing routes, all bolted, and all very short. An average climb is around 40ft, and some might get up to 90. It's the best climbing that can be done in a day trip from home, so I'm here as often as possible.
Instead of writing alot, I'll just show you a bunch of pretty pictures.
I don't suggest trying to lead a 5.12c at the end of the day when you are already tired. We both made it a little farther than this past , but kept falling back down below the hard part. After each doing the hardest part of the route a couple of times, , falling, and repeating, we gave up and got cheap greasy burgers in town.

Monday, January 26, 2009
Honey Creek Cave
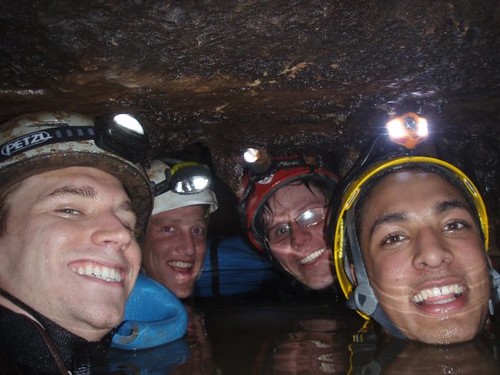
The four Aggie Cavers deep in Honey Creek Cave, the Longest Cave in Texas
Honey Creek Cave is the longest cave in Texas, with more than 20 miles of passages. The entrance is on private property, and cavers are permitted in the cave on rare occasions, so it was a special to invited on the trip. I've made it to two of the three trips that occurred since I joined the Texas Speleological Society. Honey Creek Cave has been actively explored since 1984. Most of the passages have been pushed, but one ends in a sump, which is a water filled tunnel. On the first trip I attended last year, we hauled scuab gear and a diver swam the ~1500ft sump and esstablished that it continued as a dry passage. There is rumour that it may connect to nearby caves, making it a giant network of wet and dry tunnels. The purpose of the most recent expedition was to send two divers through the sump to continue exploring the new dry passage.
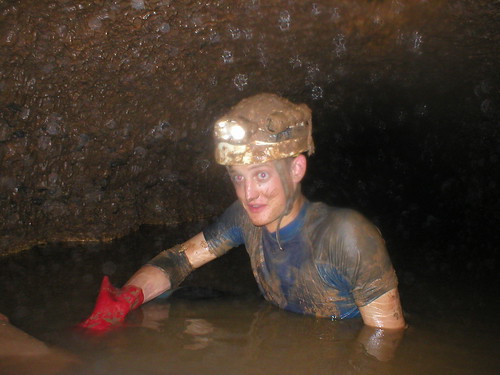
Drew cools off in the water because his 9mm wetsuit is way too hot
The cave entrance is on local property outside San Antonio, Texas. In 1984 a few Texas Cavers discovered the cave, and located a good place to drill a second manmade entrance to make it easier for cavers to access the cave. The deal was that the cavers would go in the cave, locate a spot, and drill a well for the owners allowing caver access. The well shaft was enlarged to 30" with dynamite, and a telephone pole structure was installed to allow a tractor to lower cavers down on a cable. The manmade entrance shaft puts cavers near the middle of the cave, cutting the round trip down to one long day instead of an overnight ordeal.
Krishna being lowered down the manmade entrance shaft by the tractor and cable
Most of the cave is wet and requies you to wear a wetsuit to stay warm. Cavers also need a helmet, headlamp, kneepads, harnesses, carabiners, knee and elbow pads, and a day of food and water. This cave is the "Ironman of Texas Caving." It requires virtually every caving technique there is: diving, swimming, vertical, crawling, stoop walking (which sucks btw), mud crawling, and "salamandering." Salamandering is floating on your stomach and using your hands and feet to push yourself throught he water. A Honey Creek Cave specific technique is also mud sliding.
We also volunteered to bring two suba tanks to the dive site at the sump. Each tank weighs >30lbs, and is a major PITA (Pain in the ASS) to carry. We had to carry tanks in addition to our own personal gear. There may have been 20 minutes in the whole trip where I could stand upright at all. You can't wear it like a backpack because you are constantly getting up, getting down, or crawling. On dry land where you are belly crawling, you have to push it ahead of you, or drag it behind you. Teamwork was needed to pass them over obstacles and to protect the delicate brass valve, which would be extremely dangerous if it failed. They are not such a PITA in the water because they float (due to foam padding). You can swim and push them ahead of you with your face, like a giant 3olb water polo ball.
Me with the Scuba tank (wrapped in foam to protect it)
This is one seriously tough cave. Even though it's one of the greatest adventures of caving in the Southwest, few actually sign up for trip of this magnitude. 21 cavers in total made it to the sump, each carrying loads such as Scuba tanks, Buoyancy Compensators, or cave radio pieces. Cavers came from all over, including Oklahoma, Alabama, Louisiana, Missouri, Florida, and I think Alaska too. The whole trip lasted from 9AM to nearly 2AM, or much later for the slowpokes. The trip actually went much quicker than expected.
The secondary purpose of our trip was to map the cave accurately, and to propose a location for a new entrance shaft that bypasses diving through the sump. Very few people have the gear, experience, or balls to dive a sump a days crawl away from safety. This sump is even more dangerous because of the silt, which makes the visibility just a few feet. Also, the walls of the cave are confining, making it a tight fit with all the scuba gear. We borrowed a Cave Radio, which a very low frequency closed-loop transmitter encased in rugged PVC (homemade of course) housing. It transmits one frequency, and can be received on the surface very accurately, within inches. Cavers set up the radio, and transmit for a specified period at a scheduled time. People on the surface wait for the signal on the surface, near the spot they suspect the cavers will be transmitting from. The hand measured and plotted map was used as a reference point, and the received radio point was only 60ft off! Very impressive mapping skills from the Texas Cavers. Only two of four transmissions were received well because of interference such as metal fences and barns.
At the sump. Believe or not, he is standing in water. Unlike mountaineering, the best view is not at the end of the journey!
The trip was not a complete success. One of the Scuba tanks developed a slow leak, possibly from rough handling while being dragged though miles of rocky cave. By the time everyone reached the sump, the tank was empty. Only one diver swam the sump, so that we could at least send a radio transmission from the other side. We had to wait for hours to wait for a few cavers who had missed a key turn and gotten lost to bring the buoyancy compensators. The room where we waited in for a few hours was what most sane, claustrophobic, or clean-freak people would consider muddy hell, if hell were cold and smelled like caver farts. Wetsuits are only warm if you're moving, otherwise they are frosty! I caught a quick nap in one of those foil emergency blankets and ate four of my six powerbars. With 21 people in one crowded room, the air quickly turned bad, and I suffered from a stout headache and nausea. It took every ounce of my willpower to get over my exhaustion, headache, and weak stomach to get moving away from the bad air. An old caver trick to test the air is to watch a lighter burn. The distance the flame is away from the lighter tells you the air quality. I don;t know what the normal distnace is, but the wasn't too bad, unless you were breathing it for 5 hours. Half an hour later after I got moving all my symptoms subsided and it was a sprint to the finish. Only me and one other person had trouble with the bad air. I had a lingering cold and he was devoloping the flu, so that is likely a contributing factor.
I think the worst part of the whole trip was the 34 degree weather outside. The bottom of the cave was filled with a thick fog where the "warm" (read warmer) air met the cold air. My hands froze so quickly that I could barely get my harness on or tie knots in the rope. Once I got to the surface, someone in a down coat had to help unscrew my carabiners and untie knots. I felt pretty ridiculous wearing a caving helmet, a wetsuit, and a rock climbing harness, and holding a scuba tank in the freezing weather at 2AM in the middle of the Texas plains. Cave Diving is the perfect sport for the caver-diver-mountaineer-climber who can't decide which sport is best, and settles for just looking confused to regular people. This was a pretty tough trip, but definitely one I will never forget, although I was dumb enough to do twice.
Monday, January 19, 2009
Building the Formula Hybrid Car


The engine is mostly stock (if Nascar is "stock" than so is this) so there is not too much work to do there. Our car will also have onboard engine, motor, temperature, and battery monitoring sensors as well as wheel speed sensors, GPS data logging, 3-axis accelerometers and suspension travel measurements. The software we use plots all of these on a GPS acquired map of the course, and allows us to tune the cars suspension, engine, and motor.

The Yamaha WR 250 engine, still in the bike for early tuning, with titanium exhaust

The team is working steadily, and we hope to get done in about 10 weeks. That's a tight schedule. Most teams spend a few months designing and a year building, not the reverse. However, no matter how well constructed your car is, you can't win with a bad design.
Formula SAE Driving
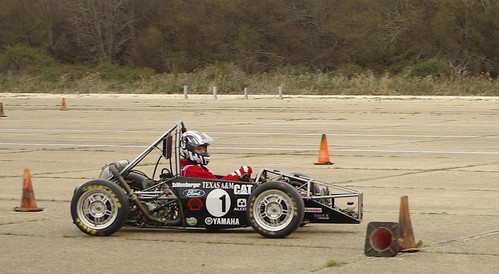

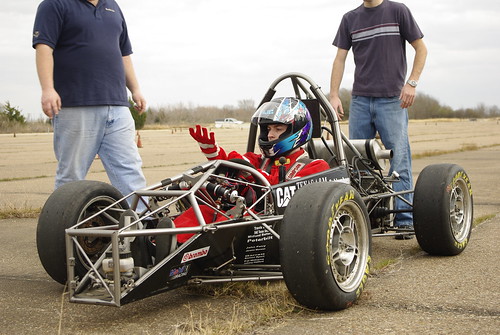