
Me and the Texas A&M 2009 Formula Hybrid car
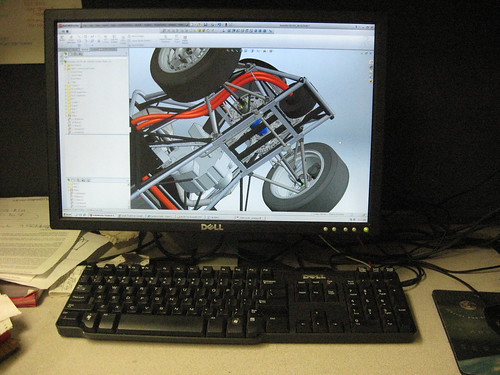
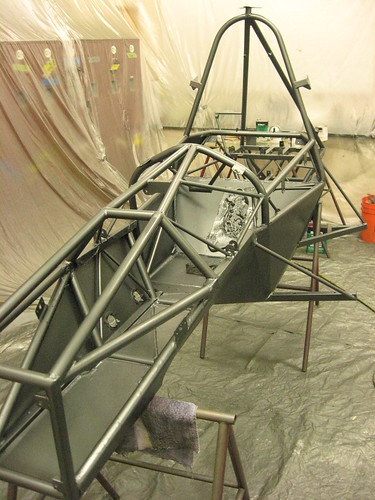
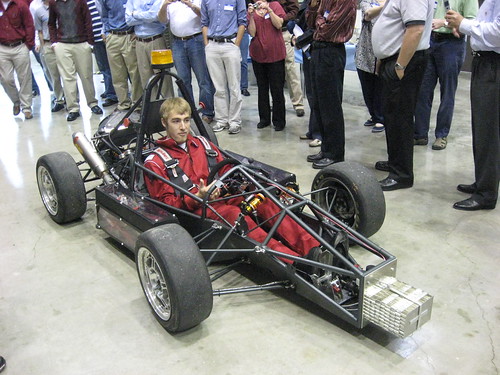
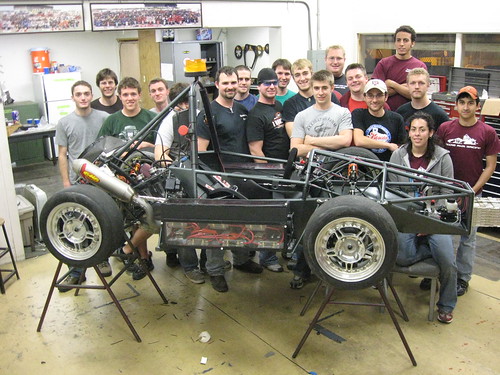
We (the Formula Hybrid team) spent the entire Spring break wrapping up the build of the car. Building takes forever because there are a million little parts, welds, and little details that were overlooked during design. Multiple parts had to remade because they didn't fit, didn't work, or interfered with other parts. There were no major screwups, but a whole lot of little ones.
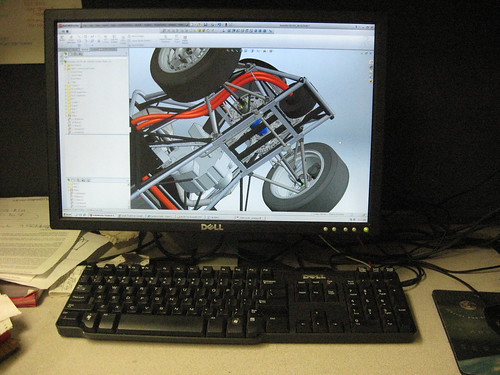
A 3d model of the hybrid powertrain
By Wednesday the build room had been converted into a paint booth, and the car was painted. The paint dried for a few days, and Friday at 5Pm we started assembling everything. While the rest of my peers were partying it up on Spring Break, we were busting our butts on this project.
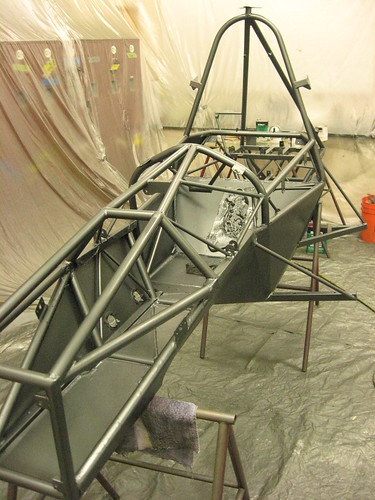
The steel space frame chassis being painted
Assembly started at 5PM and by 3AM the car was assembled and on the ground rolling. The next week was spent wiring the engine, electronics, high voltage electronics, motor, and batteries. We had a deadline of Friday, March 27th to have the car assembled. That Friday was the rollout presentation in front of a board of engineers who reviewed and critiqued our design. We were ahead of schedule, and even took the car on a test drive the night before. We were the first design team in A&M Racing's history to have a car driving under its own power at the rollout presentation.
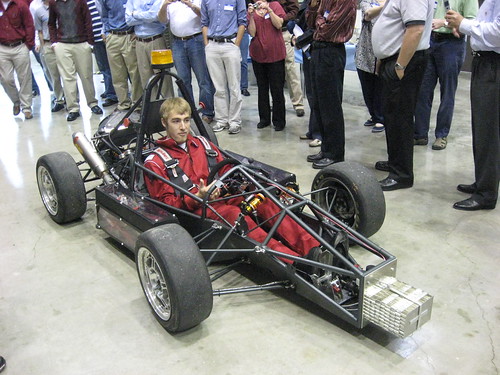
The car at the rollout presentation
This left us with just over a month to test and tune the car. Our theory is that winning teams have 1) a reliable car 2) a fast driver 3) a fast car. By getting out to drive a full month before the race day, everything that could break during competition will have already broken and fixed. The drivers will have hours and hours of experience driving this type of car and get the feel for it. So far we've had 4 hard days of testing and tuning with only 1 problem. A wheel speed sensor, which is a small metal ring resembling a gear, unbolted itself from the motor. The manufacturer right hand bolt hole in the end of the motor shaft, but it needs a left hand because the motor spins in a direction that tries to constantly unscrew the bolt. Loctite (superglue) solved the problem. Also, the carburetor keeps trying to fall off because the junky connector is plastic. It has been amazingly reliable, fast, and easy to drive considering we were all inexperienced in this and certainly none of us have ever tried to build a hybrid car before. Nobody knew for sure how it was going to perform as a hybrid because of unplanned interactions between the electric motor and the internal combustion engine. It works just as planned, despite what some of the more vocal engineers on the advisory committee thought. Next week we will be practicing for the design event and bossiness presentation, which means I still have alot of work to do. We will be driving to New Hampshire from College Station, which is a 6-day, 4,000 mile round trip. We have to tow the car, 3 sets of wheels and tires, a spare engine and motor, tire machine, full set of tools, and the welder, so we will be towing a monster trailer.
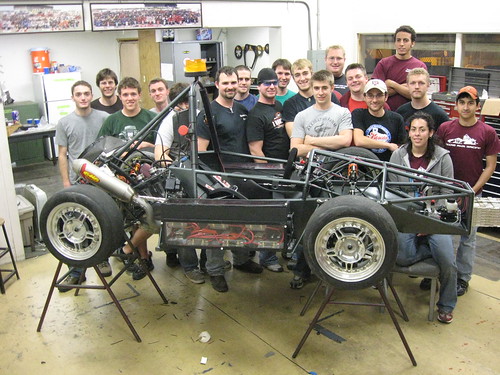
The car and the team completely assembled
Here is a little video of the assembly of the car:
No comments:
Post a Comment